In Florida, craft breweries are announcing openings, expansions, and new initiatives almost every day. The possibilities for craft beer seem limitless, except that their equipment must come from somewhere. Enter BrewFab, a brewery equipment fabricator in Saint Petersburg that is working to make high quality steel tanks and more for Florida breweries from within the Sunshine State.
When Cigar City Brewing opened their doors in 2009, the options for brewing equipment were relatively limited, especially if you wanted to keep the work on American soil. Most of those systems would have to come from the Pacific Northwest or a long way away and would need a lead time of several months. Fast forward to 2013, several years after a nationwide craft beer boom has seen the opening of dozens of breweries within Florida alone and the line for equipment has only become longer. Saint Petersburg’s BrewFab is working to keep up with the demand from Florida breweries, even if that means foregoing days off.
BrewFab is a family-owned company run by father-and-son team Rick and Kyle Cureton. Rick’s motto is simply “I have no magic, just good people working hard.” While Rick and Kyle tried to learn as much as they could from commercial brewers, they have not had very much time, as they currently have quite a few orders to contend with. When interviewed, the Cureton crew was currently building 120-barrel tanks for 3 Daughters Brewing, a new brewing system for Barley Mow Brewing, and a smaller system for the up-and-coming Stilt House Brewery. Those are the only names Rick would give, as he does not like to talk about potential clients, but at the time he had about thirty different breweries that he had quoted times and prices to.
BrewFab demands quality work from its employees, but not just as a mark of pride. After all, any tank that contains a defect or does not pass a pressure test must be scrapped and begun again from scratch. For some of the tanks that BrewFab designs, that pressure test includes some 1,800 points in each fermenter that must pass muster before the tank goes out the door. The eye for quality and consistency is one reason why it can take up to 20 weeks for BrewFab to complete and deliver a project to a client. Another reason is because BrewFab does not take a day off. Rick, Kyle, and his six other employees are working seven days a week to keep up with demand.
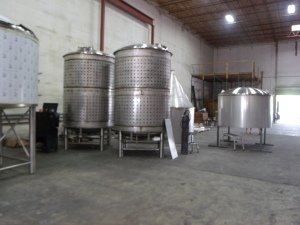
Supplying the large demand from Florida has allowed BrewFab to move into a new space in the summer of 2014. BrewFab moved from its original space into a new home The company now has a 24,000 square foot warehouse complete with 22 feet, 7 inch ceilings and an additional acre outside of an old Blocke & Transfer Storage Building built in 1898. With this new space, BrewFab will continue to manufacture equipment for the greater Florida craft breweries and beyond.
Look for BrewFab’s work at Tampa Bay breweries like 3 Daughters, Barley Mow, Stilt House, and the newly opened Angry Chair.